Managing mobile and remote assets is a significant challenge for businesses, especially when those assets are spread across different locations or in constant use. Whether it’s a fleet of vehicles, field service equipment, or valuable inventory in remote areas, tracking them in real time can be difficult.
Without clear visibility, companies face operational inefficiencies, security risks, and increased costs. Issues like asset theft, unoptimized usage, and missed maintenance opportunities can have a real impact on your bottom line.
In this blog, we’ll break down the key visibility problems businesses face with mobile and remote assets, the impact of those problems, and practical solutions to address them. Let’s dive in!
What Is Asset Visibility and Why Should You Care?
1. Asset Visibility
Asset visibility is all about knowing where your assets are, what condition they’re in, and who’s using them at any given time. In the context of mobile and remote assets, this means having clear, real-time insights into vehicles, equipment, inventory, or other assets that are in constant motion or located far from your main operations.
Having good visibility isn’t just about tracking assets on a map. It’s about connecting all the dots location, condition, usage, and performance; so you can make informed decisions. The more visible your assets are, the more control you have over them.
2. Why Is Visibility Crucial for Your Business?
- Improved Operational Efficiency: When you know exactly where your assets are and what condition they’re in, you can make smarter decisions. No more guessing or wasting time tracking things down. Whether you're sending a team member to pick up equipment or scheduling maintenance, real-time visibility allows you to act quickly and efficiently.
- Cost Savings: With full visibility, you can avoid unnecessary purchases, ensure better asset utilization, and reduce downtime. For example, knowing that a truck is already in good condition means you don't have to prematurely invest in a replacement. This helps keep costs down and extends the life of your assets.
- Security and Risk Management: Mobile and remote assets are more vulnerable to theft or damage, especially when they’re out of sight. By having visibility into asset location and status, you reduce the risk of theft and can quickly respond if something goes wrong. Real-time monitoring also helps with compliance and documentation, making it easier to meet industry standards and regulations.
In short, asset visibility isn’t just a “nice-to-have”; it’s a must-have for companies that want to optimize resources, improve security, and reduce costs .
What Are the Core Visibility Problems with Mobile and Remote Assets?
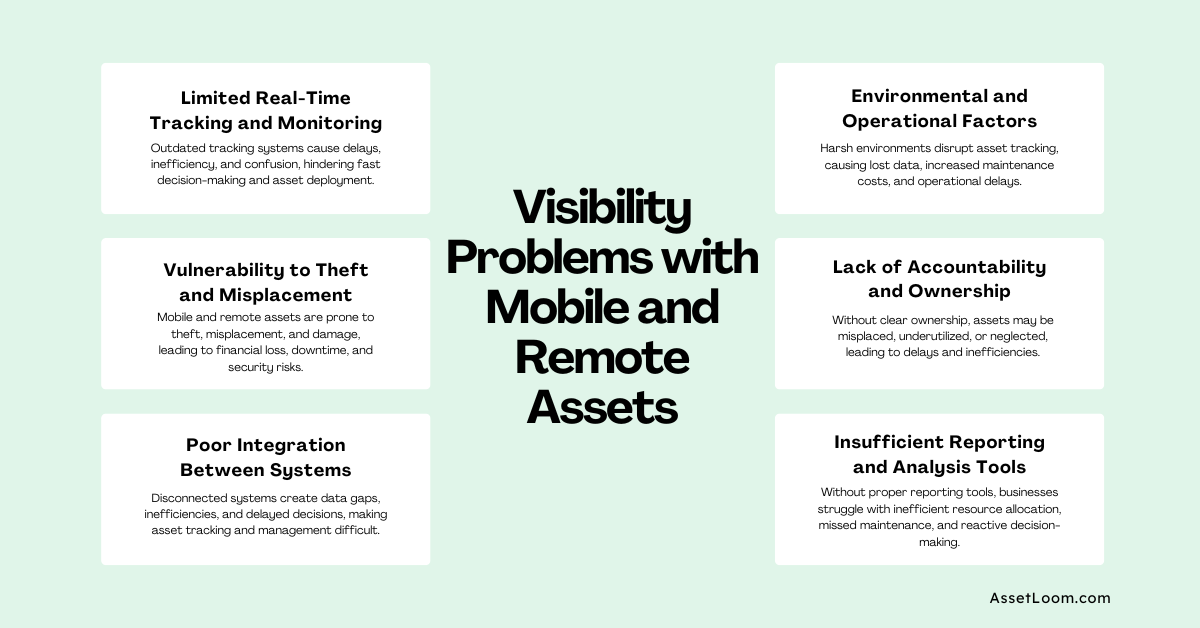
1. Limited Real-Time Tracking and Monitoring
Many businesses still rely on outdated or disconnected tracking systems for mobile and remote assets. These systems may provide sporadic updates or lack the necessary integration to give a clear, up-to-date picture of where assets are and what condition they're in.
The Impact:
- Wasted Time and Resources: Without real-time data, teams spend valuable time locating assets, which can lead to delays and inefficiency.
- Inaccurate Data: Missing or delayed updates can create confusion about asset availability, potentially leading to missed deadlines or operational disruptions.
- Operational Bottlenecks: Without the right data at the right time, operations teams can’t make fast decisions about asset deployment or reallocation.
Example: A construction company can’t locate a critical piece of machinery on-site, delaying an important project. With better real-time tracking, the location of the asset would be clear, and work could continue without unnecessary delays.
2. Vulnerability to Theft and Misplacement
Mobile and remote assets are at greater risk of theft, misplacement, or damage, especially when they are in transit or used in uncontrolled environments. Without constant visibility, it’s easy for assets to go missing.
The Impact:
- Financial Losses: Missing or stolen assets can lead to significant financial setbacks, especially when the assets are high-value or mission-critical.
- Increased Downtime: When assets are lost or misplaced, recovery can take days or even weeks, leading to prolonged downtime.
- Security Risks: Valuable equipment, particularly in sectors like healthcare or IT, may contain sensitive data or materials that need strict protection.
Example: A delivery van carrying electronics gets stolen from a warehouse. With proper asset tracking, the van’s location could be monitored in real-time, increasing the chances of a swift recovery and minimizing the impact of theft.
3. Poor Integration Between Systems
Many businesses use separate systems for fleet management, inventory tracking, and maintenance scheduling, leading to fragmented data. Without a unified system, it’s difficult to get a comprehensive view of your assets.
The Impact:
- Data Gaps: Disconnected systems create silos of information, making it hard to track asset performance or location across different platforms.
- Inefficiency: Teams waste time switching between platforms to access the information they need, leading to operational inefficiencies.
- Delayed Decision Making: Without real-time, integrated data, decisions about asset allocation or maintenance become reactive rather than proactive.
Example: A logistics company struggles to track the location of their trucks because the GPS system isn’t integrated with the fleet maintenance software. As a result, they end up dispatching trucks that are overdue for maintenance, leading to breakdowns during transport.
4. Environmental and Operational Factors
Mobile and remote assets often operate in harsh environments—be it a remote construction site, a fleet of delivery trucks in rural areas, or equipment exposed to extreme weather conditions. These environments can disrupt connectivity and tracking systems.
The Impact:
- Lost Data: Poor signal or interference from weather conditions (like heavy rain or snow) can prevent asset tracking systems from sending updates, leading to gaps in visibility.
- Increased Maintenance Costs: Assets exposed to harsh conditions may require more frequent maintenance, but without proper tracking, issues can go unnoticed until they result in expensive repairs.
- Operational Delays: Delays in getting data from assets can affect scheduling, dispatching, and maintenance planning.
Example: A fleet of trucks operating in a rural area without reliable cell service experiences tracking interruptions. This results in delayed delivery times and complicates efforts to reroute vehicles when necessary.
5. Lack of Accountability and Ownership
When assets are shared between multiple teams or locations, it’s difficult to assign responsibility. Without clear ownership or accountability, assets can be easily misplaced, misused, or neglected.
The Impact:
- Confusion Over Responsibility: When something goes wrong whether it’s an asset being misplaced, damaged, or underused; it's unclear who should be held accountable.
- Underutilization: Assets may be left idle or used inefficiently when there’s no clear ownership, leading to wasted capital.
- Operational Delays: Without clear ownership, locating and retrieving assets can take longer, affecting productivity.
Example: A piece of equipment used by multiple technicians gets damaged, but no one knows who was using it last. This lack of accountability delays repair and prevents future misuse of the equipment.
Without the right tools, businesses may not have the ability to analyze asset performance or usage patterns. Incomplete or inaccurate reports make it difficult to make data-driven decisions about asset management.
The Impact:
- Inefficient Resource Allocation: If you don’t have clear visibility into asset performance, you can’t optimize how your assets are used. This leads to either overutilization or underutilization.
- Missed Preventive Maintenance: Without the ability to track usage trends or condition reports, it’s easy to miss maintenance needs, which can result in unexpected breakdowns and costly repairs.
- Inability to Make Proactive Decisions: Lack of proper reporting means businesses are left reacting to problems rather than preventing them.
Example: A fleet manager can’t identify which vehicles are underutilized because they don’t have access to proper performance reports. As a result, they continue to operate an oversized fleet, which leads to unnecessary maintenance costs and capital expenditures.
How to Prevent These Visibility Problems
Now that we’ve explored the key visibility problems, it’s time to discuss solutions. The good news is that there are practical, tech-driven ways to address these challenges. By adopting modern tools and integrating the right technologies, businesses can significantly improve asset visibility and overcome the hurdles we've discussed. Let’s dive into the detailed solutions.
1. Embracing Real-Time Tracking with GPS and IoT Solutions
Invest in integrated real-time tracking systems, including GPS, RFID, and IoT sensors, to gain accurate, up to the minute insights into your mobile and remote assets.
Why It Works:
- Accurate Location Tracking: GPS systems provide the exact location of assets in real time, eliminating the guesswork when trying to locate an asset. This reduces time wasted searching for equipment and helps avoid operational delays.
- Condition and Performance Monitoring: IoT sensors can track an asset’s health, monitoring parameters such as temperature, fuel levels, or mechanical status. For example, if a vehicle starts to overheat or an industrial tool begins to wear down, you get a notification that allows you to address the issue before it becomes a costly breakdown.
- Enhanced Security: With GPS and RFID tags, assets are tracked wherever they go. If an asset is stolen or misplaced, you can quickly identify its last known location, improving recovery chances and reducing financial losses.
2. Integrating Systems for a Unified View
Adopt an all in one asset management software that consolidates data from various systems (such as GPS tracking, fleet management, and inventory systems) into a single unified interface.
Why It Works:
- Centralized Data Hub: Instead of having to switch between multiple disconnected platforms, a centralized system gives you one comprehensive view of all your assets. This can include location, condition, usage, and maintenance history, allowing for better-informed decisions.
- Seamless Data Flow: A unified system reduces the likelihood of data silos and ensures that all departments have access to the same, up to date information. Whether it's the field service team, the maintenance crew, or operations managers, everyone is on the same page.
- Improved Efficiency: With integrated systems, you can optimize resource allocation. For instance, you can quickly identify underused assets and deploy them where they’re needed, reducing the need to purchase new equipment unnecessarily.
3. Leveraging Cloud-Based and Mobile Solutions
Use cloud-based software and mobile apps to enable real-time access to asset data from anywhere, ensuring that your team can stay connected and informed, even when they’re out in the field.
Why It Works:
- Access Anytime, Anywhere: Cloud-based solutions allow your teams to access asset data from any device, whether they’re in the office, at the job site, or in transit. This is especially useful for businesses with mobile or remote assets that require constant tracking and updates.
- Real-Time Collaboration: Cloud platforms facilitate collaboration across teams. Field workers can update asset statuses, report issues, or log maintenance needs in real time, ensuring that operations managers and other team members have immediate access to the most up-to-date information.
- Faster Updates and Decisions: With mobile apps, field technicians can update asset conditions, check in and out equipment, and even upload pictures or notes directly into the system. This reduces the time between asset usage and record-keeping, ensuring faster, more accurate decision-making.
-> Top 10 Cloud Asset Management Software
4. Preventive Maintenance and Predictive Analytics
Use predictive analytics to proactively manage asset maintenance. By analyzing historical data and usage patterns, you can anticipate when maintenance is needed, preventing unplanned downtime and costly repairs.
Why It Works:
- Predictive Maintenance: Rather than waiting for assets to break down, predictive analytics helps you schedule maintenance based on real-time usage data. By identifying trends in asset performance, you can predict when a part might fail and replace it before it causes a system-wide issue.
- Extended Asset Life: Regular, proactive maintenance helps extend the lifespan of your equipment and vehicles. By addressing minor issues early, you can avoid major repairs that would otherwise lead to costly downtime and unanticipated costs.
- Reduced Emergency Repairs: Predictive tools help to schedule maintenance during off-peak hours, minimizing disruptions to operations. This allows your assets to be more reliable and your operations to run smoothly.
5. Implementing Accountability Features
Use systems that assign clear responsibility for each asset, ensuring that accountability is built into the asset lifecycle. Features such as user-specific asset logs, checkout/check-in systems, or ownership tags can provide clarity on who is responsible for each asset at any given time.
Why It Works:
- Clear Ownership: With accountability features, you can track which team or individual is responsible for each asset, reducing confusion over who should be held accountable if an asset is misplaced, damaged, or underused.
- Reduced Misuse or Negligence: When individuals know they are responsible for an asset, they are more likely to take care of it. Accountability tools help ensure that assets are not left idle or misused.
- Faster Issue Resolution: In the event of an asset issue—whether it’s a breakdown, damage, or loss, it’s easier to trace responsibility and resolve the problem quickly, reducing delays in getting equipment back into service.
6. Enhancing Reporting and Analytics Capabilities
Invest in reporting tools that allow for the analysis of asset performance and condition metrics. This helps operations managers make data-driven decisions about how to deploy and manage their assets effectively.
Why It Works:
- Data-Driven Decisions: Reporting tools allow you to analyze asset performance over time, enabling you to make informed decisions about resource allocation, maintenance schedules, and inventory management.
- Improved Resource Allocation: By identifying underutilized assets, you can reassign them to areas where they’re needed most, optimizing your overall asset pool and reducing unnecessary investments.
- Maintenance Insights: In-depth reports on asset health and usage trends help you identify which assets are nearing the end of their lifecycle, enabling you to plan for replacement or upgrade before failures occur.
These solutions are designed to tackle the visibility challenges head-on, providing businesses with the tools they need to optimize their asset management processes. By embracing real-time tracking, integrating systems, leveraging predictive analytics, and improving accountability, companies can not only improve visibility but also reduce operational costs, enhance efficiency, and safeguard against security risks. Platforms like AssetLoom offer businesses the technology to consolidate asset data in one unified platform, making it easier to track, manage, and analyze mobile and remote assets in real time.
Final Thoughts
Asset visibility is essential for businesses managing mobile and remote assets. Poor visibility leads to inefficiencies, wasted time, higher costs, and increased security risks. By embracing tools like real-time tracking, system integration, and predictive analytics, companies can optimize operations, reduce downtime, and improve decision-making.
If you’re managing assets, take a look at your current tracking systems. Are they giving you the visibility you need? Consider exploring platforms like AssetLoom for a unified solution to streamline asset management.